Surface treatment with maximum efficiency
Mixing, coating and drying with high-performance mixers
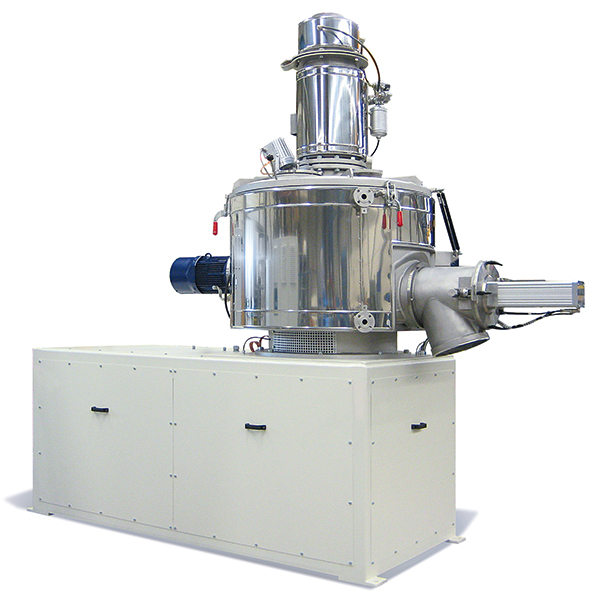
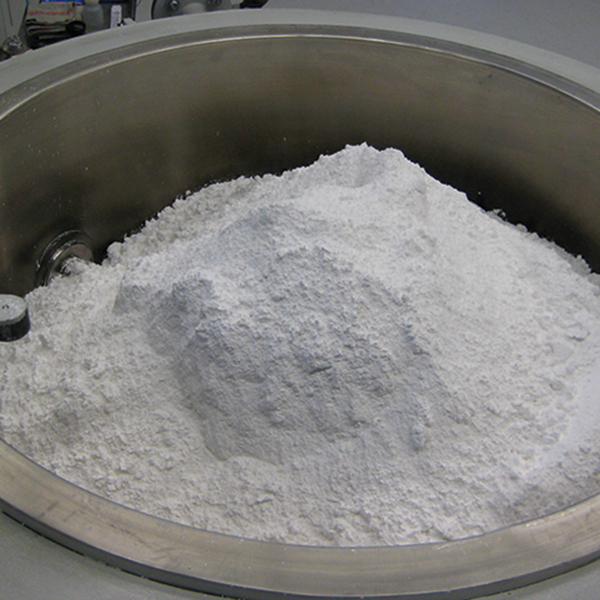
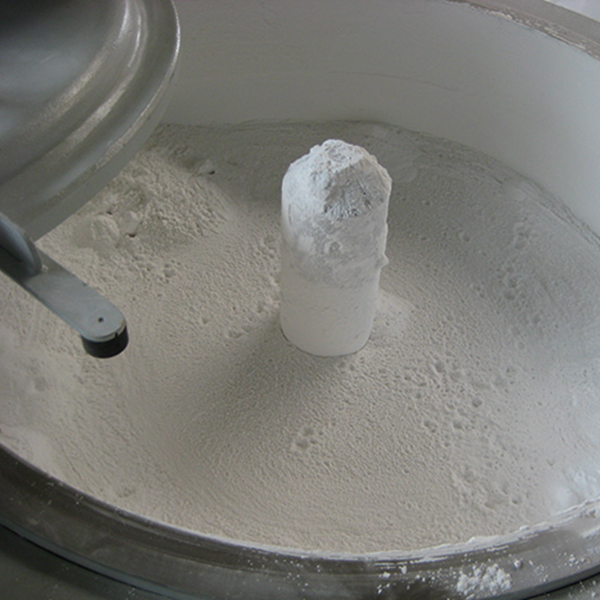
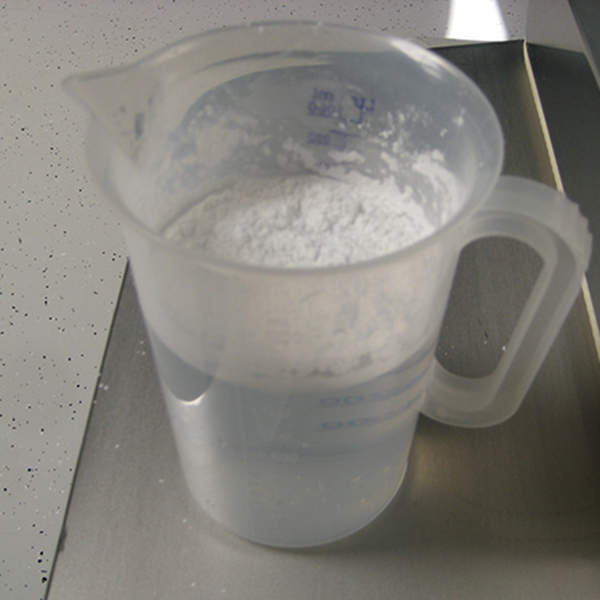
In the plastics industry, the quality of many multiphase systems depends on the formation of a good coupling between their constituents and the substrate material. For this purpose, the surfaces of minerals such as kaolin, alumina, talc, mica and quartz as well as of flame retardants such as ATH and magnesium hydroxide are coated, in most instances, with silicones and silanes. The latter are capable of binding chemically to both the inorganic substances and the organic polymers. Apart from being used as coupling agent, they may also serve as cross-linking agent, dispersion aid and rheology enhancer.
In cosmetic products, pigments, e.g., gain strong hydrophobic properties via an appropriate surface modification to reduce their water absorption. In all cases the low-viscosity coating must be applied to the surface of the inorganic recipe ingredients as homogeneously and reproducibly as possible. Such uniform and complete coating requires the use of specially optimised mixers.
Optimised effectivity, time and energy demand
A maximum flexibility can be achieved with MTI‘s practically proven Uni tec® series of high-performance mixers which provide significant advantages over conventional systems in batch processes involving mixing volumes up to 2,000 liters. At a peripheral speed of 5 – 8 m/s, their bottom-mounted mixing tool generates a threedimensional mixing vortex without dead spots wherein all particles slide off one another in a fluid bed. As a result of this intense product movement, maximum homogenisation is achieved in an extremely short time and at a very low energy demand of less than 0.05 kW of installed motor power per kilogram of mixed material.
Even in its basic equipment version, every Uni tec® series mixer can be run under vacuum in the mixing chamber. Thus, even complex process sequences can be realised efficiently and at low cost with only one machine. Vacuum drying of the minerals or pigments can be performed after the coating operation as will typically be necessary with aqueous or alcoholic solutions.
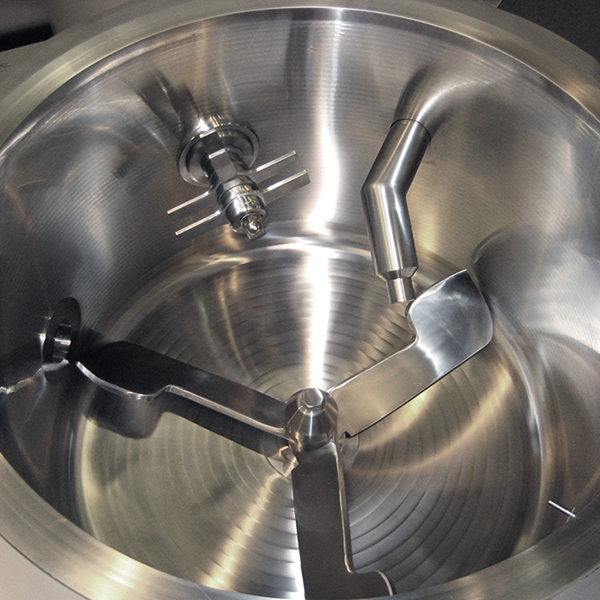
Mixing chamber with chopper and spraying system
Custom system optimisation
Where raw materials tend to build lumps, all Uni tec® mixers can be delivered with a supplementary chopper. Rotating at high speed, this tool set is fitted with blades matched to the required function. It is mounted laterally in the mixing vessel and powered by a separate motor.
Spraying systems with or without heating for adding fluids, jacket-heating of the vessel and lid, electrical surface heating and other add-on options allow the system to be tailored to product-specific requirements while ensuring an unsurpassed repeatability of the process.
Across all mixer configurations, MTI will meet the operator‘s explosion protection specifications for the mixing chamber and production environment by providing appropriately certified components. The same applies to individual hygiene standards, which are fulfilled in close coordination with the customer.
Intuitive user control
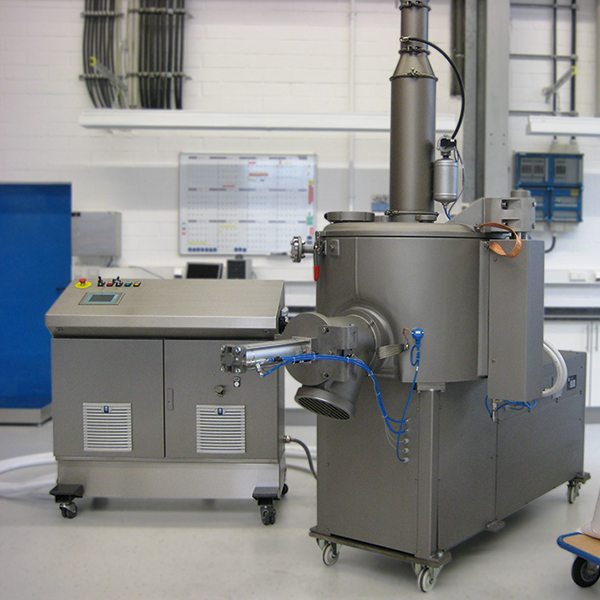
Uni tec® UT250
Intuitive machine and process control is implemented through the exclusive use of PLC-based systems. All relevant operating parameters are continuously monitored and displayed on clearly structured menu screens; this data can also be transmitted via bus interfaces for integration into local management systems including, where appropriate, accurate batch tracking.
Determining process parameters will typically call for extensive trial series. To this end, MTI Mischtechnik places a very well equipped R&D Center and the support of its experienced process engineers at the customer‘s disposal.
MTI R&D Center – We are prepared to meet these challenges
Determining process parameters will typically call for extensive trial series. To this end, MTI Mischtechnik places a very well equipped R&D Center and the support of its experienced process engineers at the customer‘s disposal.
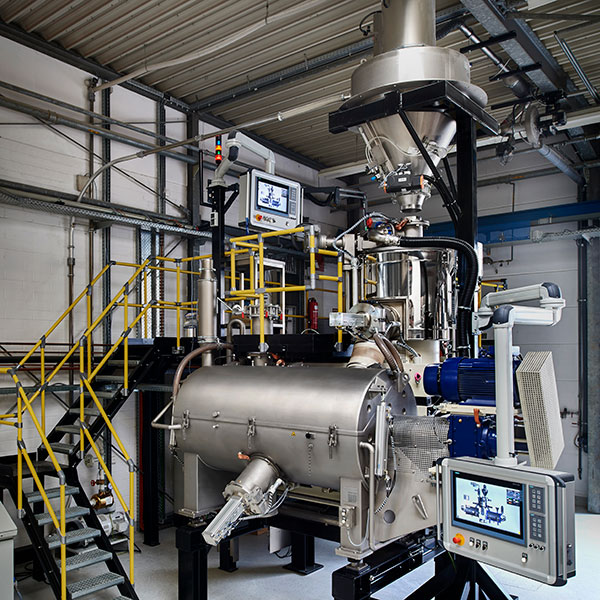
Download
Application report "Surface Treatment"
Download here the Application report "Surface Treatment" as PDF free of charge
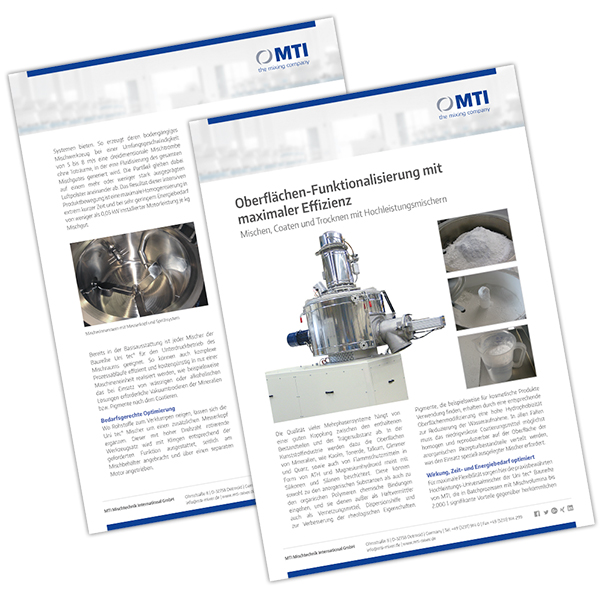
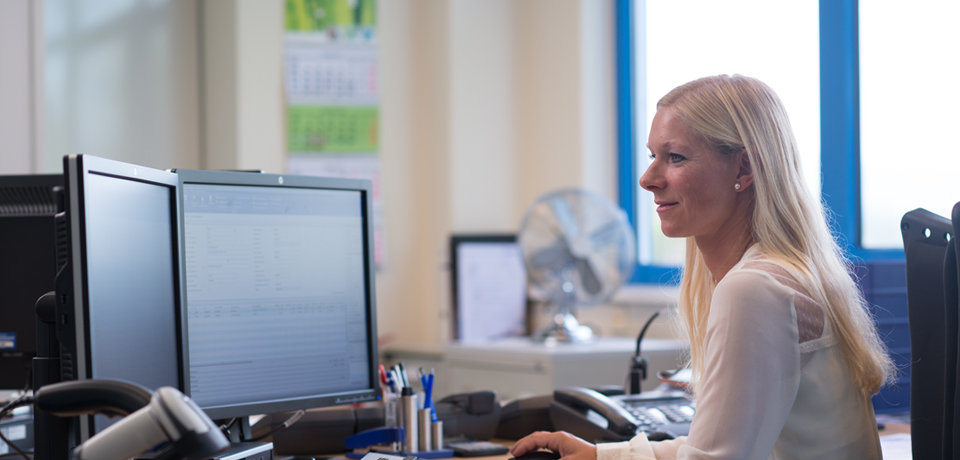